HOT PRODUCT
Suitable for express bags, clothing bags, industrial bags, bubble bags, composite bags, tablecloths, garbage bags, advertising bags, shopping bags, flower packaging, food bags, seafood bags, vest bags, etc. precision printing of plastic and paper packaging products.
ABOUT US
About Us
Guangdong Fasibang Intelligent Technology Industrial Co.,Ltd was established in 1995 and has been established for 28 years. It was originally Shantou Simapu Shanzhang Machinery Factory. After years of development, it was officially renamed "Guangdong Fasibang" in 2010. The company is located on the beautiful Rongjiang River, with a superior geographical location, only 10 minutes' drive from Jieyang Chaoshan Airport, and close to high-speed rail stations, Yongwan Expressway, and Shantou-Kunming Expressway, with convenient transportation.
View More +
Export Countries

Company established in

Employees
PRODUCTS CASE
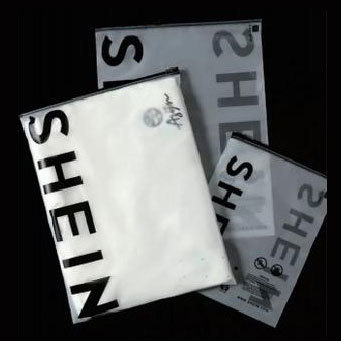
Product Case
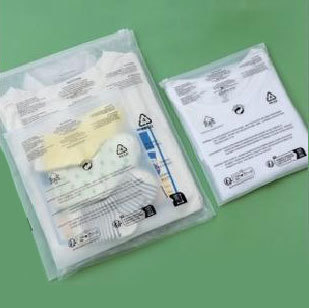
Product Case
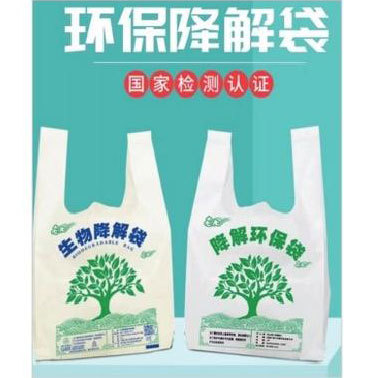
Product Case
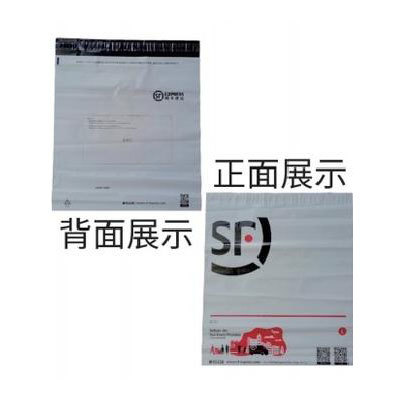
Product Case
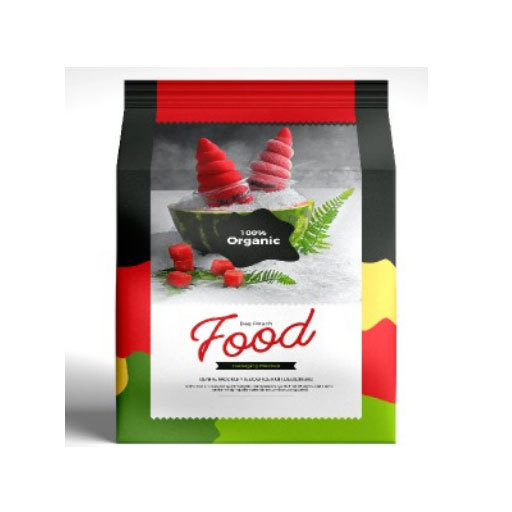
Product Case
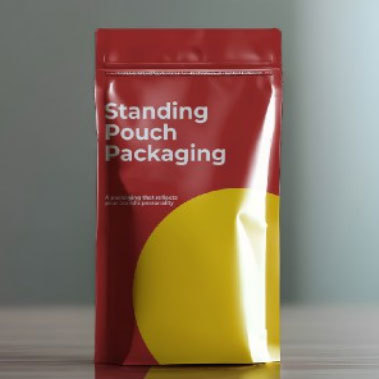
Product Case
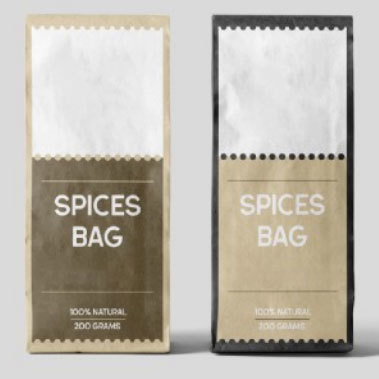
Product Case
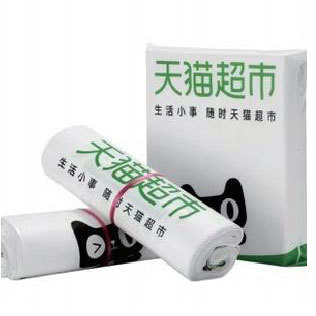
Product Case
Why Choose Us
We have a team of skilled and dedicated pre-sales and after-sales service personnel. Every machine produced by the company has professional personnel on-site installation, debugging and training to ensure that every customer can quickly master the operation method of the machine and put it into production with the highest efficiency.
Qualification Certification Advantages
★AAA Credit Enterprise ★National High-tech Enterprise ★Passed IS09001 International Quality Management System Certification
Multi-field Service Advantages
Focus on logistics, e-commerce, clothing, food, industrial packaging and other fields, providing customers with customized printing solutions.
High-efficiency Printing Technology
Using high-speed printing and intelligent automation technology, supporting multi-color overprinting and high-precision pattern restoration, adapting to water-based and solvent inks, the production speed can reach 800-1000 meters.
Service Credit Advantages
Taking "high-quality, pragmatic, and efficient" as the service tenet, adhering to the business philosophy of integrity, establishing long-term cooperative relationships with customers, and forging industry benchmarks.
Blog
The history of the printing press
What is the control principle of an intaglio printing press?
Welcome to consult our products
Submit product needs online to get more product service information.